Adelaide
City
Engineering
Your partner for special purpose machines: design, installation and maintenance
Adelaide City Engineering Pty Ltd
Head Office 101 South Terrace Wingfield South Australia 5013 Ph: (08) 8268 2562 Fax: (08) 8268 3427
Under Contruction
Adelaide City Engineering
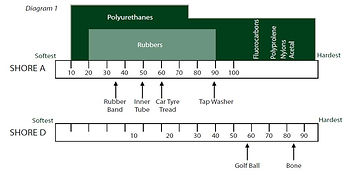
Therefore it is important to understand the application in order to correctly match the polyurethane material to suit.
Polyurethane is processed as a liquid and are applied by pouring or spraying the material into a mould or directly onto the substrate. Because the curing process involves a chemical reaction, the manufacturing process for poured polyurethane is done within heated environments where the material is cured.
Spray applications generally are not able to be heated due to the size of jobs so polyurethane spray systems are designed to cure at ambient temperatures.
Polyurethane Lined Steel Pipe
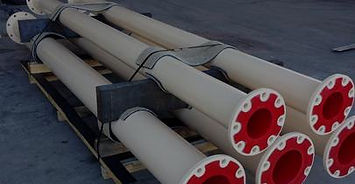
Slurry & Tailings Processing Applications
The benefits of Polyurethane lined steel pipe has become better understood within the mining sector over recent years as pipeline operators realise the cost over life benefits polyurethane provides. When specified and manufactured correctly, polyurethane pipe lines outperform competitive materials reducing maintenance and replacement costs over the operational life of the pipeline.
Polyurethane v Rubber:
Rubber remains suitable for applications where life expectancy is below five years. Where abrasion is a factor and also energy consumption, polyurethane is proven to be the most cost effective solution due to its superior abrasion resistance and low coefficient of friction, which is up to five time better than rubber.
-
Superior Abrasion Resistance
-
Lower Coefficient of Friction
-
Lower Cost Over Life
Polyurethane v HDPE:
High density polyethylene (HDPE) is a common alternative to polyurethane lined steel pipe within the mining industry. Polyurethane lined steel pipe can outperform HDPE by a factor of 3 with some installations achieving over 20 times the performance of HDPE. So while Polyurethane lined steel pipes have greater upfront installation costs, it is easy to see the cost over life benefits that can be achieved.
-
Superior Abrasion Resistance
-
Superior Impact Resistance
-
Lower Cost Over Life
Where economical to do so, polyurethane lined steel pipes can be recycled to remove the worn polyurethane and reclaim the steel.

Sewerage & Potable Water Applications
Polyurethane lined steel pipe can also provide solutions within sewerage processing facilities due to its abrasion and chemical resistance. With potable water pipe lines, specific food grade polyurethane materials can be applied. The polyurethane is also has superior impact resistance removing the need to expensive repairs than traditional concrete lined steel pipes.
To date we have manufactured straight pipe sections up to 600nb and a range of fittings such as elbows, t-pieces & reduces.
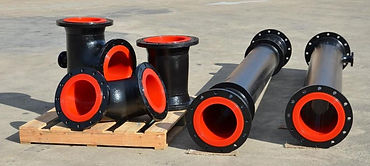
Straight pipes are rotationally cast making manufacturing of different sizes a relatively simple process. Items such as elbows, t-pieces and reduces require gravity casting process which necessitate the use of moulds.
Polyurethane Spray Coating
Polyurethane and Polyurea spray coatings are used widely in applications where abrasion, corrosion or waterproofing is required. Within the mining industry it is often used to line tanks, provide indirect wear & corrosion protection for screening frames and other equipment & structures as well as creation of membranes.
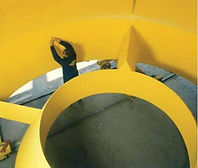
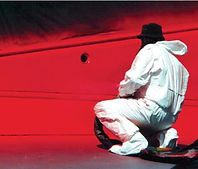
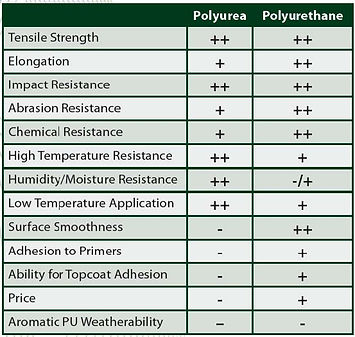

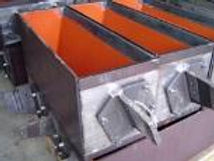
What is Polyurethane
Polyurethanes are polymeric materials containing urethane groups produced by a reaction of a polyol with an isocyanate. Polyurethane is often incorrectly classified as plastics whereas they classifying them with rubbers is more accurate due to their elastomeric nature.
Polyurethanes materials offer a number of unique engineered properties which enable products to be manufactured to meet a range of demanding applications.
There are many types of polyurethane materials available such as;
-
TDI Polyether
-
TDI Polycaprolactone
-
MDI Polyether
-
MDI Polycaprolactone
-
TDI Polyester
-
Aliphatic Systems
-
MDI Polyester
-
Polyurea Systems
Each system has its own performance advantages which extend to abrasion resistance, hydrolysis resistance, higher resilience, cut & tear resistance, oil or chemical resistance to name a few.
Polyurethane Lining
There are two varieties of sprayable material with both offering differing physical properties or characteristics making them suited to different applications. The following comparison chart briefly identifies these differences.
++ Outstanding + Good - Fair -- Poor
As spray coating applications are often large scale and performed on site, the ability to correctly prepare the surface to be sprayed and apply the coating is of utmost importance.
Access to the latest processing technology and technical support by those supplies underpins our close relationship with both material and equipment manufacturers.
Polyurethane Cast Products

Cast polyurethane products are used extensively within the mining and materials handling due to its superior combination of abrasion and impact resistance. Often used in screening media and chute linings, polyurethane has proved itself over many years to be the material of choice where abrasion occurs.
Our extensive experience over the past 20 years in supplying cast polyurethane solutions into the minerals processing industry hold us in good stead to provide a solution to any application.
Manufactured products include:
-
Screen Panels
-
Conveyor Rollers
-
Trommel Panels
-
Trommel Wheels
-
Wear & Impact Liners
-
Bucket Linings
-
Launder Sections
-
Scrapers
-
Cyclone Sections
-
Custom Mouldings

Quality Assurance / Compliance
In accordance with our ISO 9001:2008 certification, all products can be supplied with production check sheets ensure all critical processes of production (fabrication, polyurethane coating & painting) have been correctly performed.
Reports are tailored to the needs of the client and are supplied at no additional cost.
Standard testing includes:
-
Heat Certificates
-
Polyurethane Thickness
-
Weld Maps
-
Polyurethane Ratio
-
Polyurethane Hardness
-
Batch Traceability
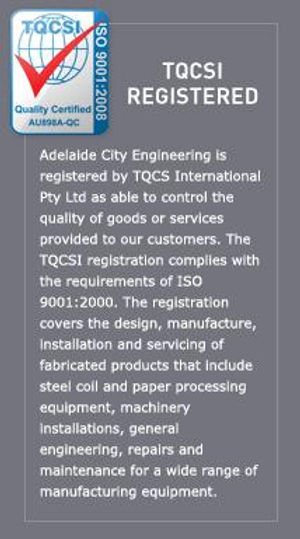